Budowa maszyn pneumatycznych opiera się na kilku kluczowych elementach, które współdziałają ze sobą, aby zapewnić efektywne działanie systemu. Na początku warto zwrócić uwagę na źródło sprężonego powietrza, które jest niezbędne do funkcjonowania tych maszyn. Kompresory powietrza są najczęściej stosowanymi urządzeniami, które wytwarzają sprężone powietrze i dostarczają je do układu. Kolejnym istotnym elementem są siłowniki pneumatyczne, które przekształcają energię sprężonego powietrza w ruch mechaniczny. Siłowniki te mogą mieć różne kształty i rozmiary, co pozwala na ich zastosowanie w różnych aplikacjach przemysłowych. Warto również wspomnieć o zaworach sterujących, które regulują przepływ powietrza w układzie oraz umożliwiają precyzyjne sterowanie ruchem siłowników. Oprócz tego, w budowie maszyn pneumatycznych istotną rolę odgrywają przewody i złącza, które transportują sprężone powietrze między poszczególnymi komponentami.
Jakie są zalety i wady maszyn pneumatycznych
Maszyny pneumatyczne cieszą się dużą popularnością w różnych branżach przemysłowych, jednak jak każde rozwiązanie, mają swoje zalety i wady. Do głównych zalet należy zaliczyć ich prostą konstrukcję oraz łatwość w obsłudze. Dzięki temu, że wiele komponentów jest standardowych, serwisowanie takich maszyn jest stosunkowo proste i niedrogie. Ponadto maszyny pneumatyczne charakteryzują się dużą szybkością działania oraz możliwością uzyskania dużej siły przy niewielkich rozmiarach urządzeń. Są także bardziej bezpieczne niż maszyny elektryczne, ponieważ nie stwarzają ryzyka porażenia prądem. Z drugiej strony, istnieją pewne ograniczenia związane z ich użytkowaniem. Przede wszystkim efektywność energetyczna maszyn pneumatycznych może być niższa niż w przypadku innych technologii, takich jak hydraulika czy napędy elektryczne. Dodatkowo, sprężone powietrze może być kosztowne w produkcji i transportowaniu, co wpływa na ogólne koszty eksploatacji.
Jakie zastosowania mają maszyny pneumatyczne w przemyśle
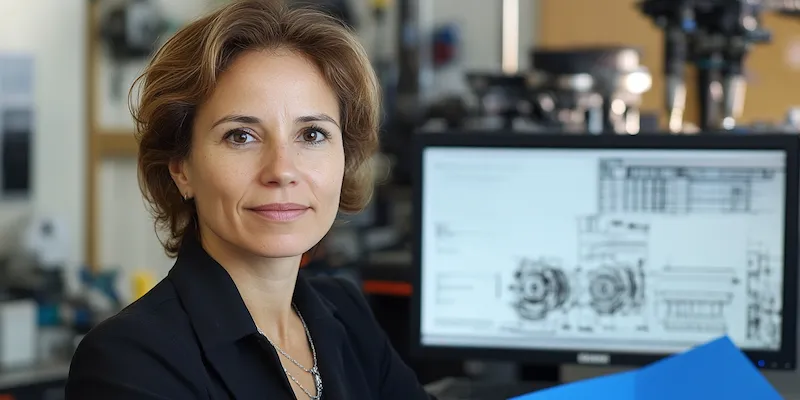
Maszyny pneumatyczne znajdują szerokie zastosowanie w różnych dziedzinach przemysłu ze względu na swoją wszechstronność i efektywność. W przemyśle motoryzacyjnym często wykorzystuje się je do montażu i demontażu części samochodowych, gdzie szybkość i siła działania są kluczowe dla wydajności produkcji. W branży spożywczej maszyny pneumatyczne służą do pakowania produktów oraz transportu surowców przez systemy rur pneumatycznych. Dzięki swojej konstrukcji są one idealne do pracy z materiałami sypkimi oraz cieczy. W przemyśle budowlanym maszyny te wykorzystywane są do podnoszenia ciężkich elementów oraz wykonywania prac wykończeniowych. Warto również wspomnieć o zastosowaniach w automatyce przemysłowej, gdzie maszyny pneumatyczne pełnią rolę napędów dla robotów przemysłowych oraz systemów transportowych. Ich elastyczność sprawia, że można je łatwo integrować z innymi technologiami oraz dostosowywać do zmieniających się potrzeb produkcyjnych.
Jakie innowacje wpływają na rozwój technologii maszyn pneumatycznych
W ostatnich latach obserwujemy dynamiczny rozwój technologii związanych z maszynami pneumatycznymi, co ma znaczący wpływ na ich efektywność oraz funkcjonalność. Jednym z kluczowych trendów jest automatyzacja procesów przemysłowych, która pozwala na zwiększenie wydajności oraz redukcję kosztów pracy. Nowoczesne systemy sterowania umożliwiają precyzyjne zarządzanie pracą siłowników oraz zaworów, co przekłada się na lepszą kontrolę nad procesami produkcyjnymi. Kolejnym ważnym aspektem jest rozwój materiałów używanych do produkcji komponentów maszyn pneumatycznych. Dzięki nowoczesnym technologiom inżynieryjnym możliwe jest tworzenie lżejszych i bardziej wytrzymałych elementów, co wpływa na ogólną wydajność układów pneumatycznych. Również innowacje związane z czujnikami i systemami monitoringu pozwalają na bieżące śledzenie stanu maszyn oraz przewidywanie ewentualnych awarii zanim one nastąpią. To znacząco zwiększa niezawodność całych systemów oraz minimalizuje przestoje produkcyjne.
Jakie są najczęstsze problemy w maszynach pneumatycznych
Maszyny pneumatyczne, mimo swojej niezawodności, mogą napotykać różne problemy, które wpływają na ich wydajność i funkcjonalność. Jednym z najczęściej występujących problemów jest wyciek sprężonego powietrza, który może prowadzić do znacznych strat energetycznych oraz obniżenia efektywności całego systemu. Wyciek ten może być spowodowany uszkodzeniem przewodów, złączy lub uszczelek, dlatego regularne przeglądy i konserwacja są kluczowe dla utrzymania sprawności maszyn. Innym istotnym problemem jest zanieczyszczenie sprężonego powietrza, które może prowadzić do uszkodzenia komponentów pneumatycznych oraz obniżenia jakości produkcji. Zastosowanie filtrów oraz osuszaczy powietrza jest niezbędne, aby zapobiec tym negatywnym skutkom. Dodatkowo, niewłaściwe ustawienia ciśnienia roboczego mogą prowadzić do nieprawidłowego działania siłowników oraz zaworów, co wpływa na precyzję procesów przemysłowych. Warto również zwrócić uwagę na problemy związane z awariami elektrycznymi w systemach sterowania, które mogą zakłócać pracę maszyn pneumatycznych.
Jakie są koszty eksploatacji maszyn pneumatycznych
Koszty eksploatacji maszyn pneumatycznych mogą się znacznie różnić w zależności od zastosowania, rodzaju urządzeń oraz warunków pracy. Na początku warto zwrócić uwagę na koszty związane z zakupem sprzętu. W przypadku maszyn pneumatycznych często konieczne jest zainwestowanie w kompresory, siłowniki oraz dodatkowe akcesoria, co może generować znaczące wydatki początkowe. Kolejnym istotnym elementem są koszty energii związane z produkcją sprężonego powietrza. W zależności od intensywności użytkowania oraz efektywności kompresora, wydatki te mogą być znaczne. Dodatkowo należy uwzględnić koszty konserwacji i serwisowania maszyn, które są niezbędne dla zapewnienia ich długotrwałego i niezawodnego działania. Regularne przeglądy oraz wymiana zużytych części mogą wiązać się z dodatkowymi kosztami, które należy brać pod uwagę przy planowaniu budżetu. Nie można zapominać o kosztach związanych z ewentualnymi przestojami produkcyjnymi wynikającymi z awarii lub konieczności przeprowadzenia naprawy.
Jakie są przyszłe kierunki rozwoju technologii pneumatycznej
Przyszłość technologii pneumatycznej zapowiada się obiecująco dzięki postępom w dziedzinie inżynierii oraz automatyki przemysłowej. Jednym z kluczowych kierunków rozwoju jest integracja systemów pneumatycznych z technologią Internetu Rzeczy (IoT). Dzięki temu możliwe będzie zbieranie danych na temat pracy maszyn w czasie rzeczywistym, co pozwoli na lepsze zarządzanie procesami produkcyjnymi oraz szybsze identyfikowanie problemów. Wprowadzenie inteligentnych czujników i systemów monitorujących umożliwi automatyczne dostosowywanie parametrów pracy maszyn do zmieniających się warunków produkcji. Kolejnym istotnym trendem jest rozwój materiałów kompozytowych oraz lekkich stopów metali, które mogą być wykorzystywane do produkcji komponentów pneumatycznych. Dzięki temu maszyny będą mogły stać się bardziej kompaktowe i wydajne energetycznie. Również rosnące zainteresowanie rozwiązaniami ekologicznymi wpłynie na rozwój technologii pneumatycznej poprzez poszukiwanie alternatywnych źródeł energii oraz metod redukcji emisji szkodliwych substancji.
Jakie są różnice między systemami pneumatycznymi a hydraulicznymi
Systemy pneumatyczne i hydrauliczne to dwa różne podejścia do przenoszenia energii mechanicznej w przemyśle, które mają swoje unikalne cechy i zastosowania. Główna różnica między nimi polega na medium roboczym; w systemach pneumatycznych wykorzystuje się sprężone powietrze, podczas gdy w hydraulicznych stosuje się cieczy hydrauliczne, takie jak olej mineralny. Dzięki temu systemy pneumatyczne są zazwyczaj lżejsze i prostsze w budowie niż hydrauliczne, co przekłada się na łatwiejszą obsługę i konserwację. Ponadto maszyny pneumatyczne charakteryzują się większą szybkością działania oraz mniejszymi wymaganiami dotyczącymi przestrzeni instalacyjnej. Jednakże systemy hydrauliczne oferują większą siłę i precyzję działania, co czyni je bardziej odpowiednimi do aplikacji wymagających dużych obciążeń lub skomplikowanych ruchów roboczych. Warto również zauważyć, że systemy hydrauliczne mogą działać w trudniejszych warunkach środowiskowych niż pneumatyczne, które są bardziej podatne na zmiany temperatury i wilgotności powietrza.
Jakie są najważniejsze standardy bezpieczeństwa dla maszyn pneumatycznych
Bezpieczeństwo maszyn pneumatycznych jest kluczowym aspektem ich projektowania oraz eksploatacji w przemyśle. Istnieje wiele standardów bezpieczeństwa, które regulują kwestie związane z użytkowaniem tych urządzeń. Przykładem takich norm jest dyrektywa maszynowa Unii Europejskiej 2006/42/WE, która określa wymagania dotyczące bezpieczeństwa maszyn oraz ich elementów składowych. Zgodność z tą dyrektywą jest obowiązkowa dla producentów maszyn sprzedawanych na rynku europejskim. Ważnym elementem zapewniającym bezpieczeństwo użytkowników jest również stosowanie odpowiednich oznaczeń CE na produktach spełniających normy bezpieczeństwa. Kolejnym istotnym standardem jest norma ISO 4414 dotycząca systemów pneumatycznych i hydraulicznych; określa ona zasady projektowania i eksploatacji tych układów w sposób minimalizujący ryzyko wystąpienia awarii czy zagrożeń dla zdrowia pracowników. Oprócz tego warto zwrócić uwagę na znaczenie szkoleń dla personelu obsługującego maszyny pneumatyczne; odpowiednie przygotowanie pracowników pozwala na uniknięcie wielu potencjalnych zagrożeń związanych z ich użytkowaniem.
Jakie są najlepsze praktyki konserwacji maszyn pneumatycznych
Aby zapewnić długotrwałe i niezawodne działanie maszyn pneumatycznych, niezwykle ważne jest przestrzeganie najlepszych praktyk konserwacyjnych. Regularna kontrola stanu technicznego wszystkich komponentów układu jest kluczowa dla wykrywania ewentualnych usterek zanim staną się one poważnym problemem. Należy szczegółowo sprawdzać przewody, złącza oraz uszczelki pod kątem oznak zużycia lub uszkodzeń; wszelkie nieszczelności powinny być natychmiast naprawiane, aby uniknąć strat sprężonego powietrza. Filtry powietrza powinny być regularnie czyszczone lub wymieniane zgodnie z zaleceniami producenta; ich prawidłowe działanie ma kluczowe znaczenie dla jakości sprężonego powietrza dostarczanego do układu. Również smarowanie ruchomych elementów siłowników powinno odbywać się zgodnie z zaleceniami producenta; niewłaściwe smarowanie może prowadzić do zwiększonego tarcia i szybszego zużycia komponentów.