Destylator przemysłowy to urządzenie służące do oddzielania składników mieszanin cieczy na podstawie różnicy w ich temperaturach wrzenia. Proces ten jest szeroko stosowany w różnych branżach, takich jak chemiczna, petrochemiczna czy spożywcza. Destylacja polega na podgrzewaniu cieczy do momentu, gdy zaczyna parować, a następnie schładzaniu pary, aby skondensować ją z powrotem w ciecz. W destylatorze przemysłowym często wykorzystuje się kolumny destylacyjne, które zwiększają efektywność procesu poprzez wielokrotne skraplanie i parowanie. Dzięki temu możliwe jest uzyskanie wyższej czystości produktów końcowych. W przemyśle chemicznym destylatory są kluczowe w procesach produkcji rozpuszczalników, alkoholi czy olejów eterycznych. Warto dodać, że istnieją różne rodzaje destylatorów, takie jak destylatory prostego i frakcyjnego, które mają swoje specyficzne zastosowania oraz zalety w zależności od potrzeb produkcyjnych.
Jakie są zastosowania destylatorów przemysłowych w różnych branżach
Destylatory przemysłowe znajdują szerokie zastosowanie w wielu branżach, co czyni je niezwykle wszechstronnymi urządzeniami. W przemyśle chemicznym są wykorzystywane do produkcji różnorodnych substancji chemicznych, takich jak kwasy, zasady czy rozpuszczalniki organiczne. W branży petrochemicznej destylacja jest kluczowym procesem przy produkcji paliw, takich jak benzyna czy olej napędowy. Destylatory pozwalają na oddzielanie poszczególnych frakcji ropy naftowej, co umożliwia uzyskanie wysokiej jakości produktów naftowych. W przemyśle spożywczym destylatory są używane do produkcji alkoholi, takich jak wódka czy whisky, gdzie istotne jest uzyskanie odpowiedniej czystości i smaku trunku. Ponadto w farmacji destylacja odgrywa ważną rolę w oczyszczaniu substancji czynnych oraz produkcji leków. W ostatnich latach coraz większą popularnością cieszą się także domowe destylatory, które pozwalają na produkcję własnych napojów alkoholowych czy olejków eterycznych.
Jakie są kluczowe elementy konstrukcyjne destylatora przemysłowego
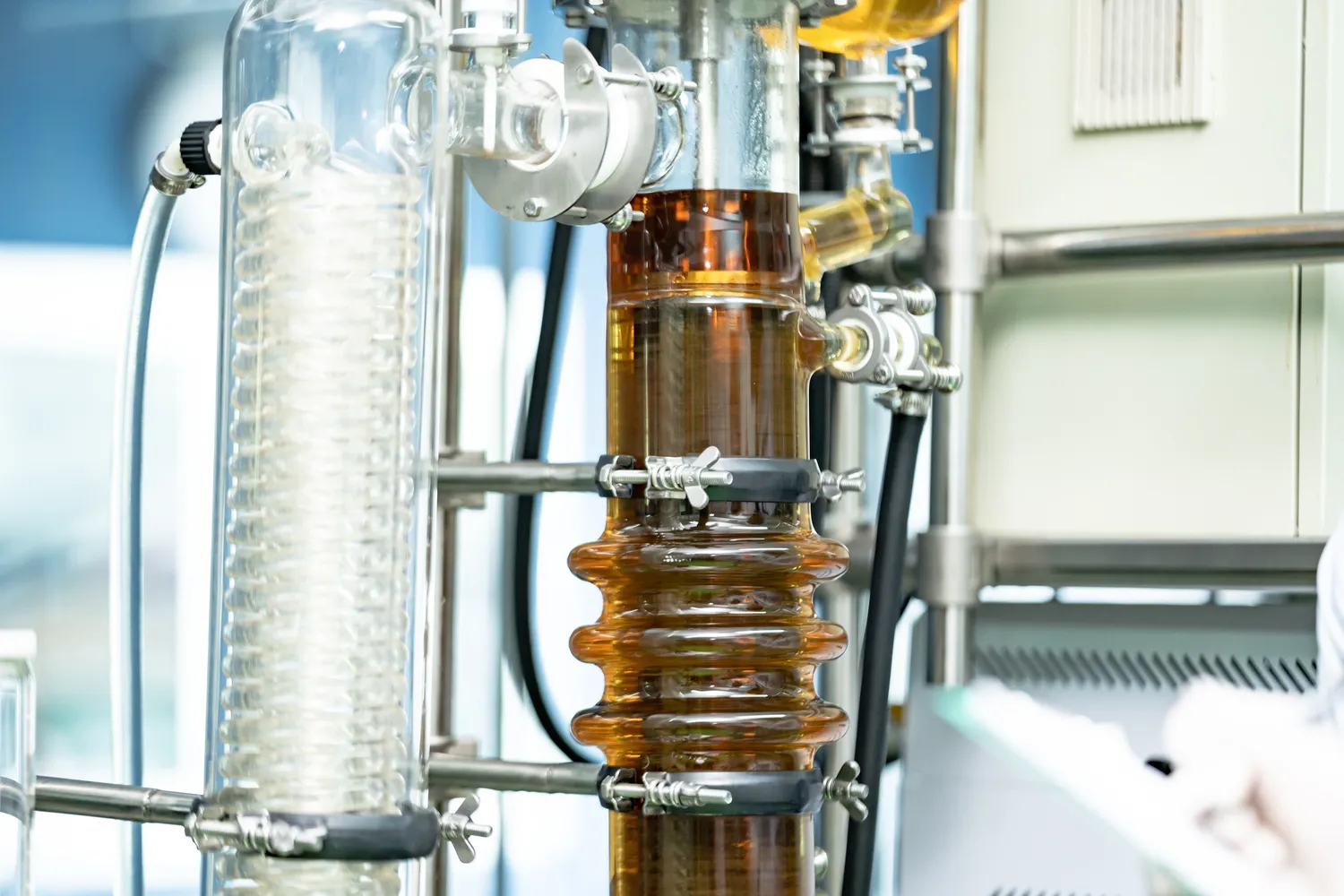
Konstrukcja destylatora przemysłowego opiera się na kilku kluczowych elementach, które współpracują ze sobą w celu efektywnego przeprowadzenia procesu destylacji. Podstawowym elementem jest zbiornik, w którym umieszczana jest mieszanina cieczy do destylacji. Zbiornik ten musi być wykonany z materiałów odpornych na korozję oraz wysokie temperatury. Kolejnym istotnym elementem jest system grzewczy, który podgrzewa ciecz do momentu jej wrzenia. Może to być realizowane za pomocą grzałek elektrycznych lub palników gazowych. Ważnym komponentem jest również kolumna destylacyjna, która zwiększa efektywność separacji składników przez wielokrotne skraplanie i parowanie. Na górze kolumny znajduje się skraplacz, który schładza parę i zamienia ją z powrotem w ciecz. Oprócz tego niezbędne są również zawory kontrolujące przepływ cieczy oraz systemy monitorujące temperaturę i ciśnienie wewnętrzne urządzenia.
Jakie są najnowsze technologie stosowane w destylacji przemysłowej
W ostatnich latach nastąpił znaczny rozwój technologii związanych z procesem destylacji przemysłowej, co pozwala na zwiększenie efektywności i oszczędności energetycznej tych procesów. Jednym z najnowszych trendów jest zastosowanie technologii membranowych, które umożliwiają separację składników bez konieczności podgrzewania cieczy do wysokich temperatur. Dzięki temu można znacznie obniżyć zużycie energii oraz poprawić jakość uzyskiwanych produktów. Innym innowacyjnym rozwiązaniem są systemy automatyzacji i monitorowania procesów, które pozwalają na bieżące śledzenie parametrów pracy destylatora oraz optymalizację jego działania w czasie rzeczywistym. Wprowadzenie sztucznej inteligencji do zarządzania procesami produkcyjnymi staje się coraz bardziej powszechne i umożliwia przewidywanie awarii oraz planowanie konserwacji urządzeń. Również rozwój materiałów konstrukcyjnych sprawia, że nowoczesne destylatory są bardziej odporne na korozję i wysokie temperatury, co przekłada się na ich dłuższą żywotność oraz mniejsze koszty eksploatacyjne.
Jakie są różnice między destylacją prostą a frakcyjną
Destylacja prosta i frakcyjna to dwa podstawowe rodzaje procesów destylacyjnych, które różnią się od siebie zarówno w sposobie działania, jak i zastosowaniach. Destylacja prosta jest najprostszą formą tego procesu i polega na podgrzewaniu cieczy do momentu, gdy zaczyna parować, a następnie skraplaniu pary. Jest to metoda stosunkowo mało skomplikowana i najczęściej używana do separacji składników o znacznej różnicy temperatur wrzenia. Przykładem może być oddzielanie alkoholu od wody. W przypadku destylacji frakcyjnej proces ten jest znacznie bardziej złożony. Wykorzystuje kolumny destylacyjne, które umożliwiają wielokrotne skraplanie i parowanie, co pozwala na uzyskanie wyższej czystości produktów końcowych. Destylacja frakcyjna jest szczególnie przydatna w przemyśle petrochemicznym, gdzie konieczne jest oddzielanie wielu różnych frakcji ropy naftowej. Dzięki zastosowaniu kolumny frakcyjnej możliwe jest uzyskanie wielu produktów o różnych temperaturach wrzenia w jednym procesie.
Jakie są kluczowe czynniki wpływające na efektywność destylacji
Efektywność procesu destylacji zależy od wielu czynników, które mogą znacząco wpłynąć na jakość uzyskiwanych produktów oraz wydajność całego procesu. Jednym z najważniejszych elementów jest temperatura, która musi być odpowiednio dobrana do rodzaju mieszaniny oraz składników, które mają być oddzielone. Zbyt wysoka temperatura może prowadzić do niepożądanych reakcji chemicznych, podczas gdy zbyt niska może skutkować niepełną separacją składników. Kolejnym istotnym czynnikiem jest ciśnienie, które również wpływa na temperaturę wrzenia cieczy. W niektórych przypadkach obniżenie ciśnienia może umożliwić przeprowadzenie destylacji w niższej temperaturze, co jest korzystne dla termolabilnych substancji. Ważną rolę odgrywa także konstrukcja kolumny destylacyjnej oraz liczba teoretycznych półek, które determinują efektywność separacji. Im więcej półek, tym lepsza separacja składników, ale wiąże się to z wyższymi kosztami budowy i eksploatacji urządzenia.
Jakie są najczęstsze problemy związane z destylacją przemysłową
Proces destylacji przemysłowej, mimo swojej powszechności i skuteczności, może napotykać różnorodne problemy, które mogą wpływać na jego wydajność oraz jakość uzyskiwanych produktów. Jednym z najczęstszych problemów jest tzw. „foul” lub zanieczyszczenie kolumny destylacyjnej, które może prowadzić do obniżenia efektywności separacji składników. Zanieczyszczenia te mogą pochodzić z resztek surowców lub reakcji chemicznych zachodzących w trakcie procesu. Innym istotnym problemem są zmiany w składzie mieszaniny surowcowej, które mogą wynikać z sezonowych różnic w jakości surowców lub błędów w procesie produkcyjnym. Takie zmiany mogą wymagać dostosowania parametrów pracy destylatora, co wiąże się z dodatkowymi kosztami i czasem przestoju urządzenia. Problemy z kontrolą temperatury i ciśnienia również mogą prowadzić do nieefektywnej separacji oraz obniżenia jakości produktów końcowych.
Jakie są koszty związane z eksploatacją destylatorów przemysłowych
Koszty eksploatacji destylatorów przemysłowych są istotnym aspektem zarządzania procesami produkcyjnymi i mogą znacząco wpływać na rentowność przedsiębiorstwa. Główne koszty związane z eksploatacją tych urządzeń obejmują wydatki na energię potrzebną do podgrzewania cieczy oraz chłodzenia pary. W zależności od rodzaju wykorzystywanego paliwa czy energii elektrycznej koszty te mogą się znacznie różnić. Kolejnym ważnym elementem są koszty konserwacji i napraw urządzeń, które wynikają z naturalnego zużycia komponentów oraz konieczności ich regularnego serwisowania. Warto również uwzględnić koszty związane z zakupem surowców oraz ewentualnymi stratami podczas procesu destylacji. Dodatkowo inwestycje w nowoczesne technologie oraz automatyzację procesów mogą początkowo generować wysokie koszty, ale długofalowo przynoszą oszczędności poprzez zwiększenie efektywności oraz redukcję strat surowców.
Jakie są przyszłe kierunki rozwoju technologii destylacyjnych
Przyszłość technologii destylacyjnych zapowiada się niezwykle interesująco dzięki ciągłemu rozwojowi innowacyjnych rozwiązań oraz rosnącej świadomości ekologicznej w przemyśle. Jednym z głównych kierunków rozwoju jest dążenie do zwiększenia efektywności energetycznej procesów destylacyjnych poprzez zastosowanie nowoczesnych technologii odzysku ciepła oraz wykorzystanie odnawialnych źródeł energii. Technologie takie jak cogeneracja czy wykorzystanie energii słonecznej stają się coraz bardziej popularne w kontekście zmniejszenia śladu węglowego produkcji przemysłowej. Również rozwój materiałów kompozytowych i nanotechnologii otwiera nowe możliwości w zakresie budowy bardziej odpornych i efektywnych kolumn destylacyjnych. Innowacje związane z automatyzacją procesów pozwalają na lepsze monitorowanie parametrów pracy urządzeń oraz optymalizację ich działania w czasie rzeczywistym, co przekłada się na wyższą jakość produktów końcowych oraz mniejsze straty surowców.
Jakie są regulacje prawne dotyczące stosowania destylatorów przemysłowych
Regulacje prawne dotyczące stosowania destylatorów przemysłowych są niezwykle ważne dla zapewnienia bezpieczeństwa pracy oraz ochrony środowiska naturalnego. W wielu krajach istnieją szczegółowe przepisy dotyczące projektowania, budowy i eksploatacji urządzeń wykorzystywanych w procesach chemicznych, w tym także destylatorów. Przepisy te często obejmują normy dotyczące emisji substancji szkodliwych do atmosfery oraz wymogi dotyczące gospodarki odpadami powstającymi podczas produkcji. Przemysł musi również przestrzegać regulacji związanych z bezpieczeństwem pracy, co oznacza konieczność wdrażania odpowiednich procedur ochrony zdrowia pracowników oraz zapewnienia im odpowiednich warunków pracy. W przypadku produkcji alkoholi istnieją dodatkowe regulacje dotyczące licencjonowania produkcji oraz sprzedaży napojów alkoholowych, co ma na celu kontrolę jakości produktów oraz zapobieganie nadużyciom związanym z ich handlem.